Direct Cylindrical Grinder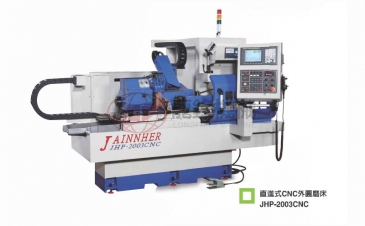
Prove once again the unique technical strength
Advanced Design Concept
1. Bearing Spindle of Direct Cylindrical Grinder (2003 A/P)
Design of High Precision and High Rigidity Grinding Wheel Spindle
The spindle sleeve group is equipped with six P4 grade high precision oblique ball bearings, four bearings at the grinding wheel end, two bearings at the belt wheel end to enhance the steering pressure of the spindle, and meticulously ancestral and rigorous testing process. The whole spindle-axle group is then adjusted by dynamic balance to reduce vibration.
2. Hydrostatic Bearing
The grinding wheel spindle is supported by 20kg/cm2 high pressure oil.
The contact friction between metal and metal is avoided, and the fog parts need not be replaced. The spindle has many advantages such as high rigidity, high precision, long service life, low vibration, low temperature rise and so on.
3. Hydrodynamic Bearing
Because the bearing and the spindle are supported by oil film, there is almost no contact between metal and metal, so the spindle will not wear and tear, and the service life will be prolonged.
The contact area between the bearing and the spindle is increased by the presence of oil film, so the best accuracy and true roundness of the workpiece can be obtained.
The oil film absorbs the vibration of the grinding process and keeps the best surface accuracy of the workpiece.
The grinding wheel spindle is supported by a low pressure oil of 3 kg/cm2.
JH70G GUI Software Fill-in Type Input with Strong Function of Direct Cylindrical Grinder! Editing and Processing Way As You Want!
1. JH70G GUI software, exploring the special programming "fill-in form" input settings, for various grinding cycle programming, is fast and convenient.
2. Explore the general program NC editing, users can edit as they like.
3. Special circular instructions can be extended to meet various processing requirements.
4. Mitsubishi CNC M70/M700 series controllers can be used to ensure accuracy and stability. And provide overseas warranty services.
5. There are four kinds of grinding cycles: basic, grinding, sand dressing and auxiliary grinding.
Diversified grinding cycle, completely based on user needs and planning! The most practical! More convenient operation!
1. Direct grinding without oscillation 2. Ticket taper compound direct step grinding 3. Direct grinding with oscillation 4. Taper taper step grinding
5. Inclined grinding 6. Shoulder straight grinding without swing
7. Compound Direct Step Grinding 8. Shoulder Step Grinding
9. Step grinding 10. Shoulder straight grinding with swing