In the process of mirror axis machining, the deformation of the axis caused by stress concentration is a key issue. The following are several effective solutions:
1、 Optimize processing technology parameters
Reasonable cutting parameters are crucial for reducing stress concentration. In terms of cutting speed, it cannot be too high or too low. If the cutting speed is too fast, a large amount of cutting heat will be generated, causing local expansion and contraction of the material, thereby generating stress. For example, for mirror axis machining of steel, the cutting speed is generally controlled within an appropriate range, such as 100-200m/min. The feed rate also needs to be finely adjusted. A too small feed rate can cause the tool to stay in the same position for too long, increasing stress. However, an appropriate feed rate can evenly distribute cutting force and reduce stress concentration. Usually, the feed rate can be set between 0.05-0.15mm/r based on factors such as shaft diameter and material. The cutting depth also needs to be carefully controlled, and multiple small cutting depths should be used to avoid stress mutations caused by excessive single cutting depth.
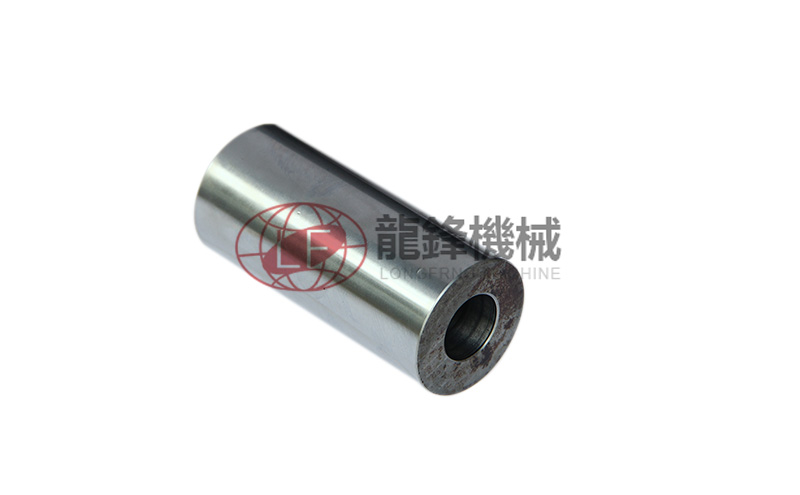
2、 Using appropriate tools and cutting methods
The geometric shape and material of the cutting tool have a significant impact on the machining stress. Choose a tool with a suitable edge radius, as a large edge radius can easily generate significant cutting forces, leading to stress concentration; If the cutting edge radius is too small, the tool is prone to wear and affect the machining quality. For example, using coated hard alloy cutting tools, the coating can reduce the friction coefficient between the tool and the workpiece, and reduce the generation of cutting heat. In terms of cutting methods, using forward milling can better reduce machining stress compared to reverse milling. During forward milling, the direction of cutting force helps to tighten the workpiece, while reverse milling tends to lift the workpiece, increasing the possibility of stress generation.
3、 Perform effective heat treatment and aging treatment
Proper heat treatment of the shaft material before or during processing is an effective measure to reduce stress concentration. For example, annealing metal materials can eliminate residual stresses inside the material. The annealing temperature and time need to be precisely controlled according to the type and performance requirements of the material. For some high-precision mirror shafts, aging treatment can also be performed after rough machining. Time treatment can make the internal organizational structure of materials more stable, further releasing residual stresses generated during the processing. For example, after rough machining, aluminum alloy mirror shafts can be subjected to aging treatment at a certain temperature (such as 150-200 ℃) for several hours, which can effectively reduce stress deformation during subsequent precision machining.
4、 Reasonable clamping method
The correct clamping method can avoid stress concentration caused by excessive clamping force. When clamping, ensure that the clamping points are evenly distributed and the clamping force is moderate. Elastic clamping devices can be used, such as hydraulic chucks, which can automatically adjust the clamping force according to the size and shape of the shaft, so that the clamping force is evenly applied to the shaft. Meanwhile, for slender mirror shafts, auxiliary support devices such as center frames can be used to reduce deformation and stress concentration caused by their own gravity and cutting forces.