The research and production of high-precision mirror axis cores is a complex and costly process, with costs mainly concentrated in the following aspects.
1、 Raw material cost
The high-precision mirror axis core has extremely high material requirements. Firstly, it is necessary to choose metal materials with good mechanical properties, such as stainless steel, high alloy steel, etc. These high-quality materials themselves are expensive because they require high strength, high hardness, and good toughness to meet the requirements of the shaft core in complex working conditions.
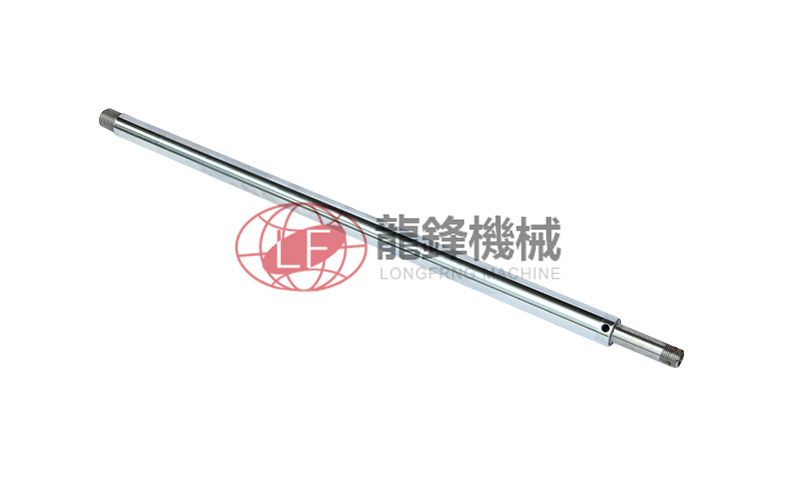
Secondly, in order to ensure the mirror effect, the purity of the material is also crucial. Materials with low impurity content help to produce smooth mirror surfaces, while the acquisition and processing costs of such high-purity materials are relatively high. For example, the purchase price of some special aerospace grade materials may be several times higher than that of ordinary steel.
2、 Equipment procurement and maintenance costs
The production of high-precision mirror axis cores requires the use of a series of high-precision machining equipment. For example, high-precision grinding machines, lathes, polishing machines, etc. These devices are expensive, and an advanced precision grinder may be worth millions. And these devices require regular maintenance and calibration during use to ensure their machining accuracy. The maintenance cost includes the cost of replacing high-precision cutting tools, grinding materials, and professional technicians for equipment debugging and maintenance.
3、 R&D and technology costs
The development of high-precision mirror core technology is a long-term and high investment process. This requires enterprises to invest a large amount of funds in technological research, including exploring new processing methods, optimizing process flows, etc. For example, developing a polishing technique that can reduce the surface roughness of the shaft core to the nanometer level requires countless experiments and consumes a large amount of scientific research reagents and materials.
At the same time, in order to maintain the progressiveness of technology, enterprises also need to introduce high-end technical talents. These professional talents have higher salaries and benefits, which are also an important component of research and development costs.
4、 Quality inspection cost
Due to the extremely high precision requirements for high-precision mirror axis cores, the quality inspection process is crucial. Enterprises need to purchase high-precision testing equipment, such as coordinate measuring instruments, surface roughness testers, etc. These devices are not only expensive, but also require professional testing personnel to operate and analyze data during use. At the same time, in order to ensure the accuracy of the test results, it is necessary to regularly calibrate and maintain the testing equipment, which also increases the cost of quality testing.
The cost of developing and producing high-precision mirror axis cores is multifaceted, requiring significant investment in raw materials, equipment, research and development, and quality inspection. This also reflects the complexity and high requirements of high-precision product production.