In the field of mirror axis machining, surface roughness is a key indicator for measuring machining quality.
Generally speaking, for mirror shafts used in ordinary industrial applications, the surface roughness requirement is usually between Ra0.2-Ra0.8 microns. This level of roughness can meet the operational requirements of most mechanical transmissions and general precision equipment. For example, in some ordinary machine tool transmission systems, such mirror shafts can effectively reduce friction, ensure stable power transmission, and to some extent resist wear, extending the service life of the shaft.
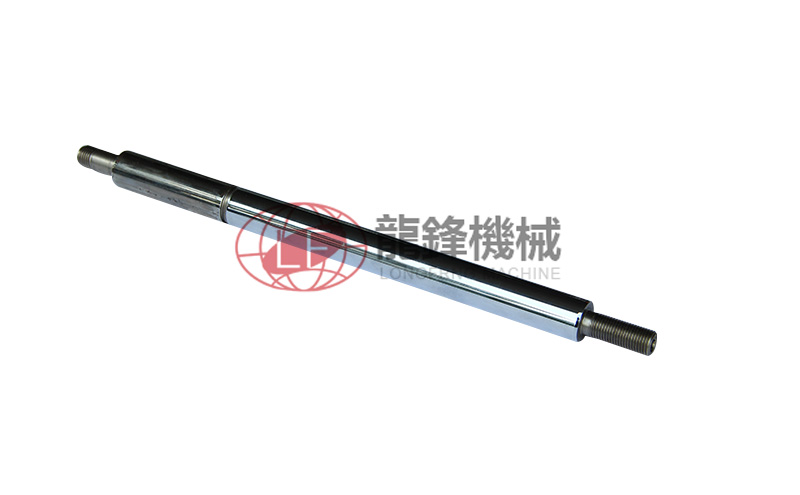
However, in high-precision equipment and precision instruments, surface roughness requirements will be more stringent. In certain key components such as optical equipment, high-precision measuring instruments, and aerospace, the surface roughness of the mirror axis may need to reach the range of Ra0.02-Ra0.1 micrometers. Taking the mirror axis in a lithography machine as an example, its extremely high precision requirement is to ensure that light can be accurately focused and reflected, thereby achieving high-precision lithography of chips. In this case, even small surface undulations can cause optical path deviations, affecting the accuracy of chip manufacturing.
In ultra precision machining applications, such as for certain high-end scientific research equipment or military equipment with almost stringent precision requirements, surface roughness is even required to reach Ra0.01 microns or below. This requires the use of special processing techniques such as ion beam polishing, magneto rheological polishing, etc. These processes can perform atomic level precision machining on the surface of the shaft, achieving a super smooth mirror effect.
Accurate measurement of surface roughness is crucial to ensure that the mirror axis meets the requirements. The common measurement method is the touch needle method, which measures roughness by moving a small touch needle on the surface of the shaft and converting surface undulations into electrical signals. There is also optical measurement method, which uses the principle of light interference to detect the surface microstructure. For high-precision mirror axes, a comprehensive evaluation is usually conducted by combining multiple measurement methods to ensure the accuracy of the measurement results.
In order to achieve the required surface roughness, it is necessary to strictly control cutting parameters such as cutting speed, feed rate, and cutting depth during the machining process. Meanwhile, factors such as cleanliness, temperature, and humidity in the processing environment can also affect the final surface roughness. Only by achieving precise management in multiple aspects such as process, equipment, and environment can mirror axes that meet the requirements of various application scenarios be processed.