The definition and measurement of precision of high-precision mirror axis core is a complex process involving multiple key elements.
1、 Dimensional accuracy
Diameter accuracy
The diameter of the shaft core is the most basic dimensional indicator. For high-precision mirror axis cores, the diameter accuracy is usually required to be in the micrometer or even sub micrometer level. For example, in some precision machining equipment, the tolerance of the shaft core diameter may be controlled within ± 5 micrometers. This means that the deviation between the actual produced shaft core diameter and the design diameter should be minimal to ensure that it can fit tightly with other components.
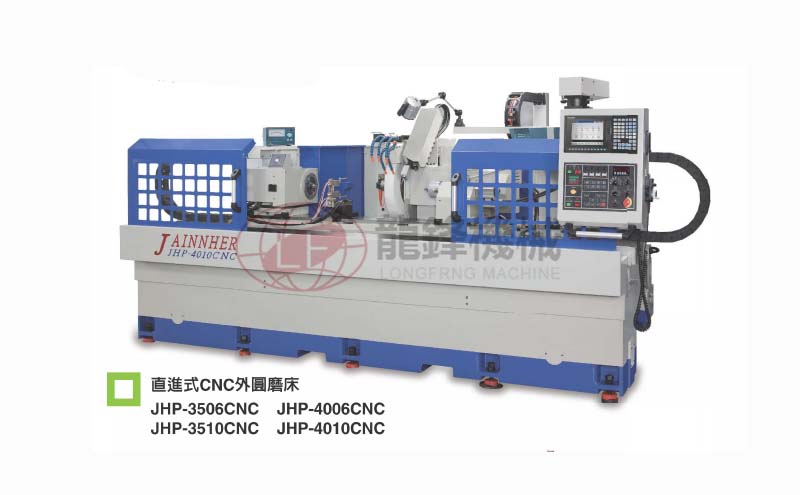
The measurement of diameter accuracy is mainly achieved through high-precision measuring tools, such as laser outer diameter measuring instruments. This instrument utilizes the principle of laser interference to accurately measure the outer diameter of the shaft core, with a measurement accuracy of about 0.1 microns, and can accurately determine whether the shaft core diameter meets the accuracy requirements.
Length accuracy
The length of the shaft core also requires high-precision control. In some application scenarios, such as in the transmission system of optical equipment, the accuracy requirements for the length of the shaft core are also very high. The length tolerance may be set within a range of ± 10 micrometers.
Length measurement can be done using calipers or coordinate measuring instruments. The three coordinate measuring instrument can accurately measure the length and other dimensions of the shaft core from three dimensions. It obtains the coordinate information of each point on the surface of the shaft core through a contact or non-contact detection head, and calculates the length and other dimensions with an accuracy of about 0.5 microns.
2、 Positional tolerance
Cylindricity
Cylindricity is a key indicator for measuring the accuracy of shaft core shape. It reflects whether the cylindrical surface of the shaft core is close to an ideal cylinder. For high-precision mirror axis cores, the cylindricity error is usually required to be controlled within 1-2 microns. For example, in a high-speed rotating motor shaft core, good cylindricity can ensure the stability of the shaft core during rotation.
The measurement of cylindricity generally uses roundness and cylindricity instruments. These instruments obtain the contour information of the shaft core surface by scanning and measuring in the circumferential and axial directions of the shaft core, and then calculate the cylindricity error.
Coaxiality
When the shaft core needs to be coordinated with other components, such as installing gears or pulleys, coaxiality is very important. Coaxiality refers to the degree of coincidence between the axis of the shaft core and the reference axis. In precision machinery, coaxiality error may be required to be within 2-3 micrometers.
The measurement of coaxiality can be achieved by using a coaxiality measuring instrument, which determines the coaxiality error by comparing the deviation between the axis of the shaft core and the reference axis.
3、 Surface roughness
Definition of roughness
For high-precision mirror axis cores, surface roughness is an important factor in measuring their accuracy. It refers to the degree of irregularity in the micro geometric shape of the shaft core surface. Usually represented by parameters such as Ra (arithmetic mean deviation of contour). In the mirror core, the Ra value may be required to be between 0.05-0.1 microns.
measuring method
Surface roughness can be measured using a roughness meter. The roughness meter records the roughness changes of the surface contour by tracing the surface of the shaft core with a stylus, and then calculates roughness parameters such as Ra to determine whether the surface of the shaft core meets the requirements of mirror accuracy.