High precision mirror core manufacturers tell you how to adjust the coaxiality?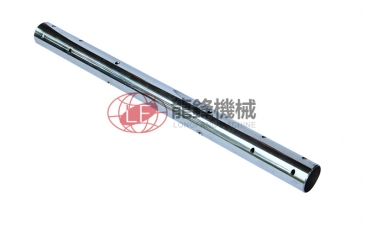
In the elevator maintenance or transformation, often encounter the scheme of replacing the motor, the more troublesome process in this scheme is to adjust the coaxiality of the motor shaft and worm shaft. So how to deal with this problem? The following high-precision mirror core manufacturers to tell you!
Because replacing a new motor is not like removing an old one and installing it as it was repaired, nor is it like removing the whole tractor and reassembling it. As long as the position and quantity of gaskets are carefully remembered during disassembly and assembly, and the gaskets are installed as they are and adjusted slightly, these two items belong to "original assembly". At the same time, matching process positioning pinholes are drilled on the motor base and tractor base, which ensures that there is no big difference between the axis deviation of motor shaft and worm shaft. Coaxiality can be quickly adjusted with the help of percentiles of radial height.
When adjusting the coaxiality of motor shaft and worm shaft, the four bolts (coupling pins) on motor shaft coupling and brake wheel coupling should not be installed first. The motor coupling is equipped with U-type magnet (which can be used in permanent magnet inductor), and 1.2-1.5Mm2 plastic copper wire is wound on the magnet. The length of the line can be as required, and then as required. Bend into a fixed angle, as shown in Figure 1 (click). One end of the copper wire is 5 - 6 mm long and 0.5 mm away from the surface of the brake wheel. Then a manual disc motor shaft is used to rotate around the surface of the brake wheel. According to the difference between copper wire head and brake wheel surface, the left and right deviation and the height difference of motor shaft are roughly adjusted. When roughly adjusting the distance between copper wire head and the surface of brake wheel lt; 0.5Mm, when touching the surface of brake wheel gently and evenly, four connecting pins are inserted into the surface of brake wheel and fixed initially. Remove the U-shaped magnet and copper wire, then calibrate the wheel with a dial gauge until it meets the requirements.
The above information is introduced by the manufacturer of high precision mirror axle core. This method has the advantages of simplicity and convenience, and solves the problem of coaxiality adjustment between motor axle and worm axle. If you need more information, please call us to consult us.