The reason why the high-precision mirror shaft core wears, the following small-scale editing of the mirror shaft processing manufacturers for everyone to introduce in detail, I hope to help everyone!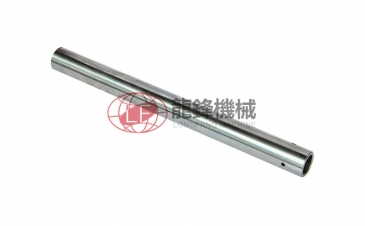
High-precision mirror core wear is the most common equipment problem in the use of high-precision mirror cores. There are many reasons for the wear of high-precision mirror cores, but the main reason is determined by the metal properties used to make high-precision mirror cores. Although the metal has high hardness, it has poor retractability (unrecoverable after deformation) and impact resistance. Poor performance and poor fatigue resistance, so it is easy to cause adhesive wear, abrasive wear, fatigue wear, fretting wear, etc. Most of the high-precision mirror shaft core wear is not easy to detect, only the machine has high temperature, large amplitude, abnormal noise When it is not the case, it will cause people to notice, but when people find out, most of the high-precision mirror cores are worn out, causing the machine to stop.
The main purpose
Precision mirror cores are widely used. In general, as long as there are motors or reducers, precision mirror cores are used. Large precision mirror cores are used in metallurgical machinery. Different precision mirror cores have different functions. The functions of various precision mirror cores are as follows: 壹, the high-precision mirror cores of the prime mover and the working machine are coupled and the torque is transmitted. Second, it is possible to properly compensate the radial high-precision mirror core and the angular error caused by the manufacturing, installation and other factors of the two high-precision mirror cores. Third, the safety of the precision mirror core when the overload occurs, the precision mirror core is slippery or the pin is broken to protect the working machine. Fourth, the elastic precision mirror core core also has the function of buffering, damping and improving the dynamic performance of the high-precision mirror core system.