How to ensure the production of qualified high-precision mirror cores
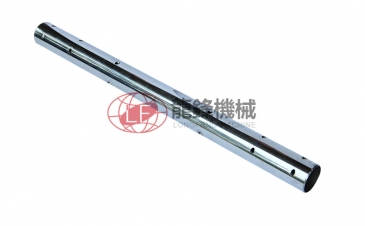
After decades of development, Chinese industry has entered the ranks of international advanced. Under such a big situation, domestic industries, whether it is automobile, communication, medical or watch, mobile phone, computer, etc., are not small. Progress and development. In such an industry, many things must be used, that is, high-precision mirror cores. Some industries require less high-precision mirror cores, and some require a lot more, and each industry needs more parts, and the use is of course not the same. Under such a large background, it catalyzes the precision machining, high-precision mirror core processing industry. Moreover, in recent years, due to the booming production and manufacturing in China, there is a demand for high-precision mirror cores, which has led to the rise of the precision machining industry. So since there are so many high-precision machining companies, there will be more or less quality problems here. Today we will talk about how to ensure the production of qualified high-precision mirror cores.
1. First, after picking up the business from the business unit, the other party needs to provide the drawings of the high-precision mirror core, and then carry out research and repeated proofing for this picture. In this project, the company engineers play a big role. Some engineers look at the drawings basically blink of an eye, while some technicians look at the drawings with deviations. Therefore, the first step is very important, the first step is not good, and the latter is mostly in vain.
2, the choice of materials, there is a saying: quality is good, the material is very important. In general, the materials needed for precision machining are stainless steel bars, copper bars, aluminum and so on. This does not require a good quality control, or it will be produced at the time, and it will be easily damaged and worn. Of course, in order to reduce costs, some companies choose materials that are also low in price, so that they are making money, but the problems that arise in the later period will be great. In addition, the cutting oil used in the processing, and the cutting fluid, the quality of this flaw is not much.
3, processing equipment, this link is mainly, the purchase of CNC machining equipment, in general, imported parts of the equipment processed parts will have less deviation, low scrap rate, and high productivity. Nowadays, the equipment imported from Europe, America and Japan is a good choice.
4, of course, the best equipment, and the best materials also need excellent operators to operate. Of course, it is best to have employees who work with high-precision mirror cores all the year round.
5, Finally, the quality inspectors, after each part of the production of the parts, must be inspected and tested by the quality inspectors to pass the test, can be considered completely passed, to achieve the above points, basically a qualified part is counted out. Of course, there are also transportations that need to be noted. After all, some materials are soft, and if they are too much squeezed, they are easy to be damaged.
Basically, the above five points are completed, so there is no problem in producing a qualified high-precision mirror core.